Image intensifier tubes are the technology at the core of night vision devices. These sophisticated components amplify available ambient light, transforming the invisible into a visible world. An image intensifier tube is essentially a vacuum tube with a photocathode at one end and a phosphor screen at the other. When photons of light strike the photocathode, they release electrons. These electrons are then accelerated and focused onto a microchannel plate, which amplifies the electron stream. Finally, the amplified electrons strike the phosphor screen, producing a visible image.
Different Generations of Image Intensifier Tubes
The evolution of image intensifier tubes has been marked by significant advancements in technology, leading to distinct generations with varying capabilities:
Gen 0: While not technically a generation, Gen 0 refers to early experimental image intensifier tubes with extremely limited performance. They were plagued by issues like low light gain, short lifespan, and poor image quality.
Gen 1: The first commercially available image intensifier tubes, Gen 1 offered a noticeable improvement over Gen 0. However, they still suffered from drawbacks such as haloing (a bright ring around objects), phosphor burn-in, and limited lifespan.
Gen 2: A significant leap forward, Gen 2 tubes introduced microchannel plate technology, dramatically increasing light amplification and image quality. Haloing was significantly reduced, and lifespan was extended. Gen 2 tubes also became more sensitive to a wider range of light wavelengths.
Gen 3: Building upon the foundation of Gen 2, Gen 3 tubes incorporated advancements in photocathode materials and microchannel plate technology. This resulted in even higher light amplification, superior resolution, and increased sensitivity. Gen 3 tubes also exhibited reduced noise and improved image clarity.
Below is an illustration of the difference in image intensifier tube generations (Rogalski, Antoni & Chrzanowski, K. 2014. “Infrared Devices And Techniques (Revision).” Metrology and Measurement Systems).
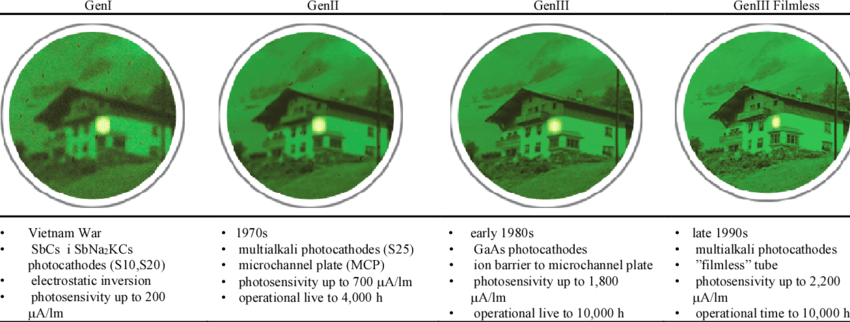
Different Uses for Image Intensifier Tubes
Image intensifier tubes and their corresponding devices are, of course, commonly used by military and law enforcement personnel. These devices enable troops and law enforcement officers to operate effectively in low-light and no-light conditions. Night vision equipment also helps hunters track or observe wildlife, and it allows outdoor enthusiasts enhanced visibility during activities like camping. Image intensifier tubes are used in surveillance cameras and security systems to monitor and detect threats.
Less common applications of image intensifier tubes include scientific research; in astronomy, they help capture faint celestial objects, and in industrial processes, they are used to inspect materials and equipment in low-light environments. Image intensifier tubes can also be used in specialized medical imaging equipment to enhance visualization of certain procedures.
The Challenges of Manufacturing Image Intensifier Tubes
Manufacturing image intensifier tubes is a complex and demanding process that requires incredible attention to detail and stringent quality control. Numerous factors contribute to these challenges.
Image intensifier tubes operate in a near-perfect vacuum. Achieving and maintaining this level of vacuum during manufacturing is extremely difficult and requires specialized equipment and cleanroom conditions. Any contamination or gas molecules within the tube can degrade performance and lifespan. The components within an image intensifier tube are incredibly fragile. They require careful handling and precise assembly to avoid damage. Even microscopic particles or imperfections can significantly impact performance. The materials used in image intensifier tubes must be of exceptionally high purity to ensure optimal performance. Impurities can reduce the efficiency of the photocathode, degrade the microchannel plate, or diminish the brightness of the phosphor screen.
Achieving consistent performance across a large number of tubes is challenging. Variations in material properties, manufacturing processes, and assembly can lead to differences in image quality, light amplification, and other critical parameters. The specialized equipment, materials, and labor required for image intensifier tube manufacturing contribute to high production costs. This, combined with the need for extensive quality control, makes these components relatively expensive compared to other electronic components. Image intensifier tubes are sensitive to environmental factors such as temperature, humidity, and magnetic fields. Protecting them from these influences during manufacturing, transportation, and operation is crucial.
Compared to mass-produced electronic components, image intensifier tubes are manufactured in relatively small quantities. This can lead to higher costs and longer lead times.
Future Trends and Advancements in Image Intensifier Tube Technology
There is ongoing research to develop image intensifier tubes that surpass Gen 3 performance, offering even higher sensitivity, resolution, and dynamic range; advanced signal processing techniques and materials engineering will be employed to further reduce noise and improve image clarity.
While still in its infancy, there is potential for developing image intensifier tubes capable of capturing and displaying color information in low-light conditions.
There’s a growing demand for smaller, more compact image intensifier tubes to integrate into wearable devices, drones, and other compact systems. Image intensifier tubes may be integrated with other technologies to create hybrid systems offering enhanced capabilities. Researchers are also exploring the potential of 3D printing for creating complex image intensifier tube components.
As you can see, the development of new image intensifier tube technologies is a complex and time-consuming process. Many challenges, such as maintaining ultra-high vacuum conditions and ensuring the reliability of delicate components, will continue to be significant hurdles. Despite these challenges, the ongoing research and development efforts in image intensifier tube technology are expected to lead to continued improvements, expanding the range of applications for this critical technology.